Back to Product Category
OVERHEAD BRIDGE CRANE
REMOTE CONTROL SYSTEMS
|
|
PATRIOT |
|
|
|
|
|
|
|
The
most affordable, high quality remote crane control
available from the Patriot® brand. 100% American
made and supported, the Patriot® is offered in four
models, all of which use Patriots proven Command
Pro® technology. All Patriot systems are shipped ready
to install with a six foot long wiring harness and include
our exclusive extruded aluminum receiver enclosure.
Best of all, the Patriot series transmitters come with a
One Year Unconditional Warranty! |
|
|
|
|
|
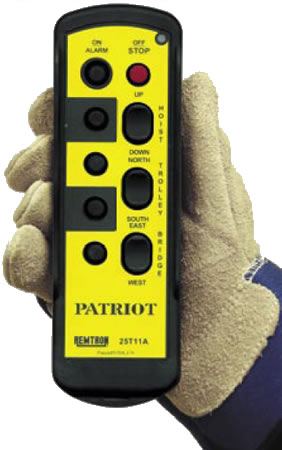 |
|
|
|
|
|
|
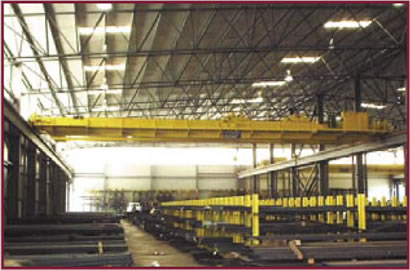 |
|
|
|
|
|
|
|
|
|
HIGHLIGHTS |
|
|
|
|
|
|
compact and
extremely tough keypad operator control
A rugged and reliable system means less downtime
Superior factory support with an unconditional one-year warranty
Made entirely in the USA |
|
|
|
|
|
|
|
|
|
|
|
|
HIGH-VALUE,
RELIABEL CRANE CONTROLS |
|
|
|
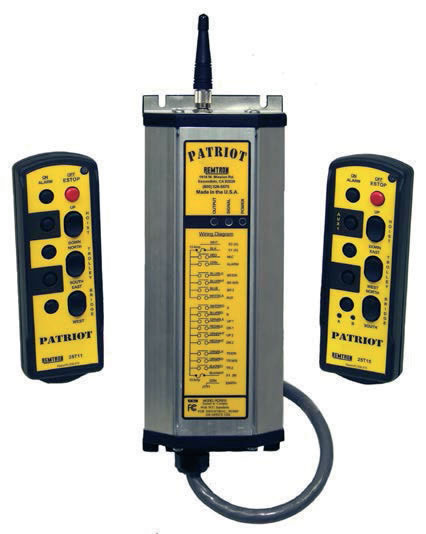 |
|
|
|
|
See
below Prices for Configuration Sheets and Specifications |
|
|
|
FEATURES |
|
|
|
Up to 15 Functions
On/Alarm and Off/Stop Buttons
Up to 3 Two-Step Discrete Rockers
Up to 6 Push Buttons
Optional Multiplex Selector
LED for Operational Status
Long-life disposable batteries |
|
1 Year
Unconditional TX warranty
TX Leather Holster & Strap Not Included
Standard TX Labels Supplied
120 VAC Receivers
NEMA 12 Enclosure
No Transfer Switch on Receiver
10-foot Pigtail |
|
|
|
|
|
|
APPLICATIONS |
The
systems are built to survive in aggressive industrial environments. |
|
|
|
|
|
|
|
Overhead
Cranes
Heavy Machinery
Ship Loaders |
|
Metal Fabrication
Amusement Parks
Lifting Equipment |
|
|
|
|
|
|
|
COMPLIANCE |
UL508
Electrical Safety |
|
|
|
|
|
|
|
|
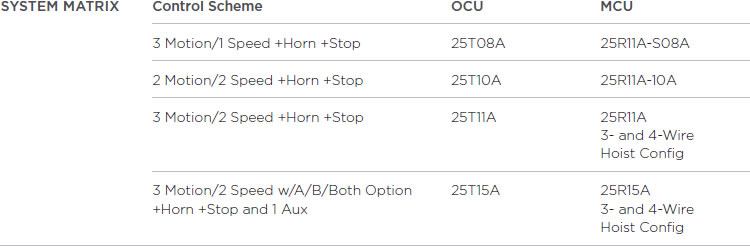 |
|
|
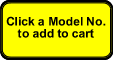 |
|
Order
Online, by Phone, or by E-Mail |
|
|
|
~ Add
items to your online shopping cart ~
Click the Model No. of the item you wish
to purchase. |
|
|
|
|
|
|
Prices |
Model No. |
Description |
Price |
Three-Motion/One-Speed Cranes |
|
25T10A Transmitter and 25R11A Receiver |
$1,308.33 |
Two-Motion/Two-Speed Monorails (Not for use on Ramp & Hold) |
|
25T10A Transmitter and 25R11A Receiver |
$1,391.67 |
Three-Motion/Two-Speed Cranes |
|
25T11A Transmitter and 25R11A Receiver Includes:
-Control for 3 or 4 wire hoist configuration
-Outputs for the M/L and Alarm |
$1,658.33 |
4 or 5 Motion/Two Speed Cranes W/ A/B/Both T/H Selector |
|
25T15A Transmitter and 25R15A Receiver Includes:
- Control for 3 or 4 wire hoist configuration
- Outputs for the M/L and Alarm - A/B/Both software for T/H selection
- One momentary auxiliary output |
$2,083.33 |
Options |
|
Additional 1 year Extended Warranty, Handheld Transmitter |
$166.67 |
|
Note:
The 25S15A system selects auxiliary T/H(s) using a P/B selector and requires
pilot relays.
For spares and aftermarket parts, please see below. ~ Spare
transmitter price at time of system order.
*Only available at time of original
sale. |
|
TECHNICAL
DATA AND SPECIFICATIONS |
|
|
|
|
|
|
ELECTRONIC
DATA |
|
MECHANICAL
DATA |
Commands See matrix on front
Digital circuitry Microprocessor technology
System addresses 16-bit, 65,535 unique addresses
Energy-saving mode Automatic shutdown
(15 minutes)
Supply voltage 2- AA batteries
Autonomy >130 hours typical |
|
|
|
|
|
|
OCU |
MCU |
|
Weight |
T10A
0.25 kg ( 9 oz) |
--- |
|
|
|
|
|
T11A/T15A
0. 28 kg (10 oz) |
|
|
|
|
|
|
Dimensions
L x W x H |
T10A
7 x 16.5 x 2.5 cm
(2.8 x 6.5 x 1 in) |
25.4x12.7x6.4
cm
(10 x 5 x 2.5) |
|
|
|
OPERATION
AND INDICATION |
|
|
|
|
|
|
|
|
|
|
|
|
|
Actuators |
Up
to 3 dual step rocker switches,
horn, stop, Aux and A/B/both |
|
|
T15A
7 x 20.5 x 2.5 cm
(2.8 x 8.1 x 1 in) |
|
|
|
|
|
|
|
|
|
|
LED |
1
status LED for active, low battery |
|
|
|
|
|
|
|
|
|
|
Housing |
High-impact,
fiber-reinforced
nylon |
Aluminum |
RF |
|
|
|
|
|
|
|
|
|
Frequency
range |
902-927
MHz
85 RF channels |
|
|
|
|
|
|
|
|
|
IP67,
suitable for
outdoor use |
IP52,
suitable for
indoor use |
|
|
|
|
Transmitter output power 1mW license exempt |
|
|
|
|
|
|
Modulation |
Packet
Mode, FM |
|
|
|
|
|
|
|
Operating
temperature |
-29°
to +71° C |
(-20°
to +160° F) |
|
|
|
RF
channel spacing 300 KHz |
|
|
|
|
|
|
|
|
|
Antenna |
Internal |
|
|
|
|
|
|
|
|
Vibration
and
shock |
Vibration/impact
and drop
tested to 1m on concrete |
|
|
|
FCC
ID |
T10A
style
EGT810TX (25T10A) |
|
|
|
|
|
|
|
|
|
|
ACCESSORIES |
|
T18A
style
ECT818TX (25T11A, 25T15A) |
|
|
|
Batteries |
2-
standard AA |
|
|
|
|
|
|
3-motion/1-speed
25S08 - 25T10A Transmitter and 25R11A Receiver |
|
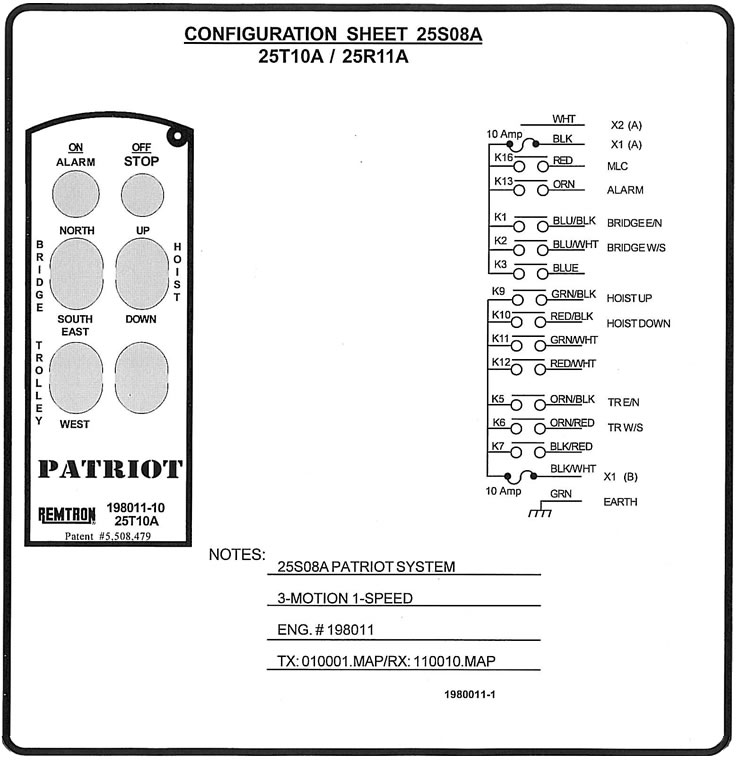 |
|
2-motion/2-speed
25S10 - 25T10A Transmitter and 25R11A Receiver |
 |
|
3-motion/2-speed
Cranes 25S11A - 25T11A Transmitter and 25R11A Receiver |
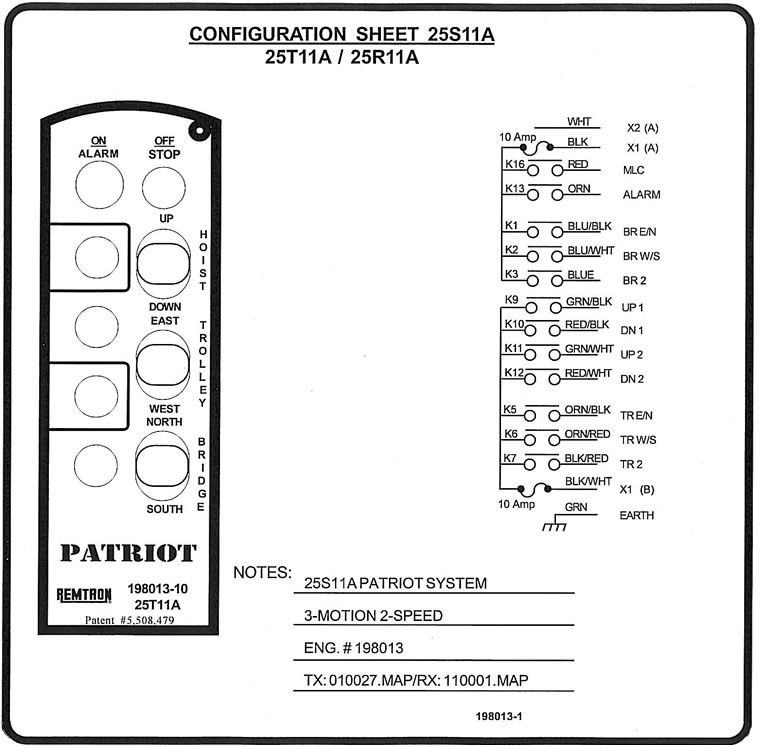 |
|
4
or 5-motion/2-speed Cranes W/ A/B/Both T/H Selector 25S15A -
25T15A Transmitter and 25R15A Receiver |
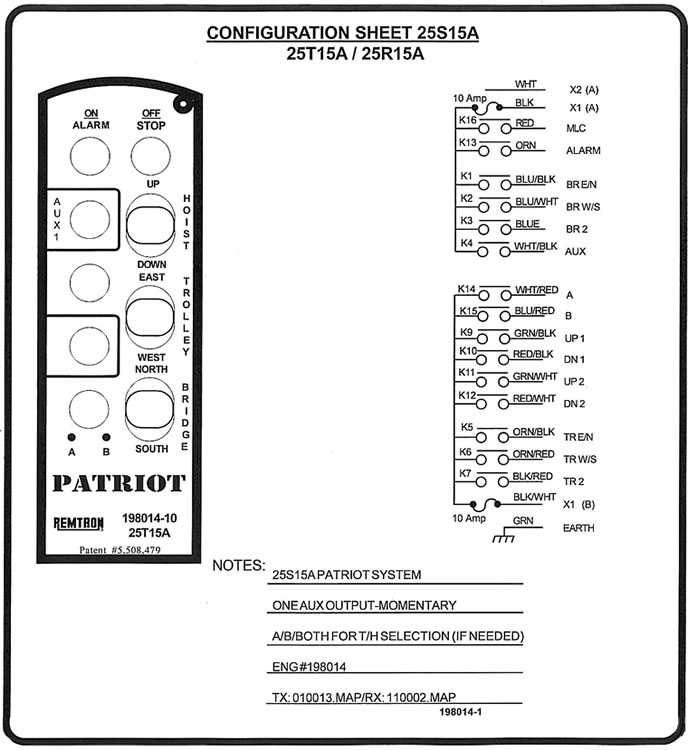 |
Tech
Note
IP Ratings Explained |
|
The
IP Code defined in international standard IEC 60529 classifies the level
of protection that electrical appliances
provide against the intrusion of solid objects or dust, accidental contact,
and water. It consists of the letters IP (for
"international protection rating"[1], sometimes also interpreted
as "ingress protection rating") followed by two digits
and an optional letter.
The digits indicate conformity with the conditions summarized in the tables
below. Where there is no protection rating
with regard to one of the criteria, the digit is replaced with the letter
X.
For example, an electrical socket rated IP22 is protected against insertion
of fingers and will not be damaged or
become unsafe during a specified test in which it is exposed to vertically
or nearly vertically dripping water. IP22 or
IP2X are typical minimum requirements for the design of electrical accessories
for in-door use. The standard aims to
provide users more detailed information than vague marketing terms such
as "waterproof".
Patriot transmitters are IP66/67 rated. Below is a break down of what IP66/67
is in relation to our
products.
First digit:
The first digit indicates the level of protection that the enclosure provides
against access to hazardous parts (e.g.,
electrical conductors, moving parts) and the ingress of solid foreign objects. |
|
Level |
Object protected against |
Effective against |
6 |
dust tight |
No ingress of dust; complete protection against contact |
|
|
Second
digit:
Protection of the equipment inside the enclosure against harmful ingress
of water. |
|
Level |
Object protected against |
Details |
6 |
powerful water jets |
Water projected in powerful jets against the enclosure from any
direction shall have no harmful effects. |
7 |
immersion up to 1 m |
Ingress of water in harmful quantity shall not be possible when
the enclosure is immersed in water under defined conditions of pressure
and time (up to 1 m of submersion). |
|
IP
codes are similar to NEMA ratings. Equivalent NEMA ratings for Patriot products
with IP ratings:
NEMA 4 Water Tight & Dust Tight - Indoors/Outdoors
Type 4 enclosures are intended for general purpose indoor or outdoor use
primarily to provide a degree of protection
against windblown dust and rain, splashing water, and hose directed water;
and to be undamaged by the formation
of ice on the enclosure.
NEMA 6 Submersible, Water Tight, Dust Tight, & Ice/Sleet Resistant
- Indoors/Outdoors
Type 6 enclosures are intended for general purpose indoor or outdoor use
primarily to provide a degree of protection
against the entry of water during temporary submersion at a limited depth;
and to be undamaged by the formation of
ice on the enclosure. |
|
Technical
Note
Infrared Wireless Control |
|
Infrared
(IR) has advantages and disadvantages for the use in remote control. Infrared
radiation is electromagnetic
radiation whose wavelengths are greater than those of visible light but
shorter than those of microwaves. In its most
familiar form, it is radiated heat which can be sensed by our skin, yet
cannot be seen by our eyes. All objects, what-
ever their temperature, emit infrared radiation. Like light and unlike radio
frequency (RF), IR is very directional and
is usually focused into a beam for best propagation. RF propagates in all
directions depending on the polarization of
the antenna and, especially at lower frequencies, can bend around
objects. The primary advantages of using IR in
remote control are: 1) no requirement for licensing or FCC certification
for use in license free bands, 2) relatively
low cost and, 3) safety restrictions that require the user to be close to
the receiver (usually less than 150 feet) and
in direct sight of the receiver. The disadvantages especially over RF control
systems include the following;
1. Directionality At moderate distance, IR systems require
an operator to aim the hand held unit in the direction
of the receptor. If on a crane, this is toward the bridge and upward. The
most significant operating problem
introduced is the fact that an operator must split his attention between
thinking of aiming constantly, verses, thinking
of moving the object involved.
2. Range IR has very limited reliable range compared to RF.
IR tends to become intermittent at distances over
100 feet.
3. Sun Light The IR component of the sun can interfere with
the IR signal. The receiver must be shaded from
the sun. In outdoor use the receiver must be installed to avoid direct or
reflected exposure from the sun. This is
particularly difficult at dawn and dusk and in very bright and reflective
environments.
4. Weather IR is attenuated by dust, smoke, rain and fog that
will substantially reduce operating range. The
receiver lens must be frequently cleaned and protected from rain, frost
and ice to avoid further attenuation of the
signal.
5. Cluttered Work Environments IR requires line-of-sight from
the transmitter to the receiver unlike RF.
Operators cannot control the equipment if vehicles and other obstructions
are between the transmitter and receiver.
6. Emergency Stop Response In an emergency, the operator must
acquire the receiver before sending an
emergency stop command which delays shutting down equipment. RF is almost
instantaneous.
7. Safety Link RF can maintain a constant link from the transmitter
to the controlled equipment (maintained
link) and automatically shutdown the equipment if the transmitter
fails or the batteries fail. Normal IR systems are
not capable of a maintained link mode and will continue last
command if the transmitter fails.
8. Night and Low Visibility Operations Operators have difficulty
acquiring the receiver if the receiver location
is hard to locate.
9. Interference There can be interference noise that is disruptive
to IR signals, some common sources are
lighting systems, heaters, and especially strobe lights used on mobile vehicles. |
|
Technical
Note
Intrinsically Safe |
|
Patriot
provides specially produced versions of selected models of our products
for use in hazardous environments.
These products are qualified as intrinsically safe. What does
that mean? Extra safety is required in environments
that include flammable gases, vapors, liquids, or dust. For electronic equipment,
the requirement is to eliminate any
point in the electronics that could be an ignition source. Depending on
the nature of the combustible environment, the
ignition source must be kept well beneath the combustible initiation temperature
of gas and dust in the environment.
Gases such as propane, and dust such as metals, coal, and grain, have their
own combustion temperatures. In some
highly combustible environments, we also can seal the electronics in enclosures
that contain combustion and prevent
it from igniting the local environment. Patriot defines intrinsically
safe in terms of Underwriters Laboratories (UL)
standards. Depending on the model, Patriots intrinsically safe products
are rated UL Class I, Division 1 and Groups
C and D; Class II, Division 1 and Groups E, F and G; and temperature code
T3.
Class Class I includes environments of flammable gases,
vapors, or liquids. Class II includes combustible dust.
Division 1 This is the most stringent division of either
class. It covers situations where ignitable concentrations of
flammable gases, vapor, or liquids (Class I) and combustible dust (Class
II) can exist all of the time or some of the
time under normal operating conditions.
Groups This specifies the type of flammable substance
in the hazardous environment. We are qualified in five
groups: C (ethylene), D (propane), E (metals), F (coal), and G (grains).
T3 This is a temperature code and rates the equipment
for environments of less than 200 degrees C.
Patriot uses the Intrinsically safe (2-fault) method as defined in UL 913
(US) and CSA-157 (Canada) to achieve
this level of safety. These standards specify the design and constructional
requirements and test procedures for
equipment and parts of equipment intended for use in hazardous locations
and also for associated equipment intended
for use in safe locations. Each product that is rated carries a unique label
that specifics the rating, operational limits,
and instructions for maintaining the rating. Patriots intrinsically
safe processes are inspected quarterly by ETL to
maintain our listing. |
|
Technical
Note
Battery Life |
|
Some operators have
experience with transmitters that only last for one work shift or about
10 hours and then require
recharging. Remtrons transmitters last over 130 hours of operation,
depending on the model. That typically means
months of operation without being interrupted by a dead battery. Long
battery life makes a big difference in how you
operate and whether you need a rechargeable unit or can use standard,
off-the-shelf AA batteries.
Why do Patriot transmitters last so much longer than other wireless transmitters?
The secret is in the design.
Patriot transmitters are designed to be very frugal with the available
battery power. We use the following three
design techniques to greatly extend battery life:
Efficient Packet Mode Transmission - Transmitting
is the largest drain on battery power. Our Command Pro
transmitters operate in the 900 MHz band, where wideband operation is
feasible. Many competitors operate in the
400 MHz band or lower, where narrow-band transmission is required to get
the needed operating range. Operating
wideband allows a lot of data to be sent in a very short time. This in
turn means that packet mode transmission can
be used to send data in a short burst. Then the transmitter turns off
until a new data packet is to be sent. Furthermore,
using a data compression scheme that greatly decreases the transmitted
bytes necessary to convey the necessary
information further reduces transmission time. A transmitter that is turned
on only for short periods of time requires
less power to transmit data. Most of our competitors operate in a narrow
band that requires almost continuous
transmission to get the data sent.
Circuit Design Efficiency - Our transmitter circuits are
designed to be very efficient. The microprocessor is used
sparingly and the transmitter is powered on only when sending data. Further,
if no new data needs to be sent (no
change in command switch positions), the transmitter duty cycle is further
reduced to the minimum that will safely
keep the system alive.
Smart Battery Management - A battery power converter is
used so that the maximum amount of power can be
withdrawn from each cell before its useful life is expended. If a linear
regulator is used to derive power from a
battery, up to 70% of the available energy in the battery may be wasted.
The power converter allows about 92%
of the power to be withdrawn.
Our Command Pro transmitters boast the longest battery life in the industry.
It was a goal during the design of
the Command Pro series to minimize the battery issues. Most industrial
remote controls require rechargeable
batteries, with their inherent problems, or require the purchase of expensive
specialized batteries from the manu-
facturer. In most cases, the batteries do not have very good battery life.
For the convenience of our customers,
Patriot designs its transmitters to use commonly available AA cells. Our
transmitters also accept rechargeable
AA batteries. |
|
Technical
Note
Safe-T-Range - Controlled Range System |
|
With
the advent of lower-cost wireless control systems for material handling
equipment, end users are becoming
increasingly aware of the potential for cranes to be operated from unsafe
distances. Today, most wireless remote
control manufacturers are offering their equipment on high frequency, unlicensed
bands that dont require the
complicated licensing procedures of the past. With higher frequencies comes
the ability to operate a crane from a
distance of 300 to 1000 feet, which has caused some companies to search
for a solution to this safety concern. An
increasing number of companies industrial safety departments are requiring
range-limited controls for the safe
operation of their cranes, machinery, and other material handling equipment.
New solutions have been developed
that offer different ways of controlling the distance at which the operator
can operate the crane. The following are
a few of the techniques now available:
Infrared Control Infrared control is commonly used
in household consumer items such as remote-controlled TVs,
VCRs, and stereo equipment. With infrared control, in order to maintain
control, the operator must keep in constant
contact with the crane by physically pointing the transmitter at one or
more infrared eyes on the crane. While this is
effective, infrared control still has long-range capabilities, and the requirement
to continuously point the transmitter
at the crane is often seen as a safety concern in itself. Infrared control
is also susceptible to plant dust and bright light
such as sunshine, which can interrupt signals and cause crane movement to
be stopped intermittently.
Infrared Start/RF (Radio Frequency) Control Controlling
the range is also popular in Europe, where a tech-
nique called Infrared Start/RF (Radio Frequency) Control is used. This technology
uses an infrared transmitter and
receiver to start the crane main line contactor. Once the crane is started,
long-range radio frequency is then used to
control the crane motions. While this is believed to be a better way of
controlling a crane, limitations still exist.
Specifically, the tendency is for the operator to start the crane in close
proximity to it but then operate it at a much
farther distance, which defeats the purpose of keeping the operator close
to the crane at all times. The shortcomings
of infrared are again an issue with this type of system.
RF Range Control The industry has shown that radio frequency
control is the preferred means of controlling
a crane and other material handling devices. RF is able to transmit around
corners and is free from the issues of
dirt or other airborne particles. However, with the very low power of todays
unlicensed transmitters and the very
high frequencies that are being used comes a very long-range signal that
is difficult to control. But with todays
microprocessor technology, manufacturers are able to manage these RF signals
to the end benefit of the operator
and their safety.
We offer an RF-controlled range system called Safe-T-Range that is
not affected by modern automation
devices like Variable Frequency Drives (VFDs) or electronic discharge machines
commonly used in manufacturing
processes. The system can be custom-adjusted to the end users range
requirements, usually in the 30 to 100 ft.
range. The receiver monitors the power of the signal received from the transmitter
to determine the distance
between the operator and the equipment. The receiver may be programmed to
allow an operator to leave his safety
circle only for a short time period before he must return to the safety
zone. An indicator light or horn tells the operator
he is out of range and must return to his safety circle of operation.
If he does not return, the crane is brought to a
safe stop. The end user can decide which functions he wants to range control.
For example, an operator may need
controlled range on the Hoist and Trolley but need a long range on his bridge
motion for calling the crane from the
end of a long bay. Of course, all safety functions may remain enabled even
if all other functions of the crane are
range-inhibited. |
|
Command
Pro Technical Note
Safety of Operation |
|
Safety
is a special requirement of industrial wireless control systems. Other wireless
systems such as cellular phones,
car keyless locks, pagers, and even garage door openers dont have
the safety concerns that face the wireless
operation of cranes or construction equipment. The design of industrial
wireless controls must have additional features
that reduce the probability of injury to operators and damage to equipment
or material. Our Command Pro
systems are designed specifically for this use and have the following features
that address each potential hazard:
False Command Prevention Wireless control receivers
must be designed to accept only valid commands,
and those valid commands must come from only one authorized transmitter.
Spurious signals from any other RF
energy source should not be misinterpreted as a command. Nor should the
receivers accept commands from any
other transmitter except the one that is registered and in control of the
equipment. We developed a very
unique design that is solely for controlling equipment and for the reception
of the Patriot specially formatted
signals in an industrial environment. Each command or packet is subjected
to error checking using Cyclic
Redundancy Codes (CRC) to prevent false commands. More than 64,000 unique
address codes assigned to 82
frequencies are available using Patriots 16-bit address code. This
results in over 5 million unique identifiers.
For the transmitter to work, the unique identifier must be registered with
the receiver.
Inadvertent Command Prevention The transmitter
should not transmit a command unless the operator
makes a purposeful action to issue a command. Patriot protects the controls
during operation from inadvertent
commands by using a protective ridge around the unit. Critical commands
such as load release are protected by
requiring the operator to press two rocker switches simultaneously and hold
them for a couple of seconds. After
that time interval, the receiver implements the command. For further protection,
the unit times out when not being
used and must be turned back on to activate the controls. Time-outs may
be set very short if a push-to-operate
(PTO) control must be pressed for each command. For special concerns, Patriot
provides a Safety-T-RangeTM
feature that limits the distance from the receiver at which the operator
can issue commands to the system.
Emergency Stop Override In the event of an emergency,
there must be a simple and readily accessible
command that will take precedence over all other communications, stop the
controlled equipment, and place the
equipment in a safe mode. Patriot provides an ESTOP button on all Command
Pro transmitters. The ESTOP
overrides all commands and has priority communication to the receiver. Once
received, the ESTOP command
triggers the receivers safety circuit to implement a three-step shutdown
procedure. The first step opens the motor
relays and stops movement of the equipment.
Interrupted Transmission Failsafe In the event
that the receiver loses the command signal from the
transmitter, the receiver must take action to place the controlled equipment
in a safe mode. Patriot uses a
continuously transmitting protocol (maintained link) with the receiver that
includes a failsafe watchdog timer. If
the receiver does not receive a valid command in less than 60 milliseconds,
it goes into shutdown mode.
Shutdown mode is programmed to go through three phases that safely bring
the equipment into a safe state of
operation.
Receiver Failsafe - In the event the receivers
electronics fail or lose power, the relays that control the
equipment must fail to a safe mode of operation. Patriot has a special safety
circuit in each receiver that
automatically shuts down operations if the microprocessor fails or if power
is lost to the receiver. The relays
themselves are designed to fail to the open position, which effectively
disrupts the commands and halts
operation.
Our customers include major amusement parks and industrial plants that depend
on
Patriot systems as their primary emergency shutdown system. |
|
Technical
Note
Spread Spectrum |
|
Patriot does not use spread spectrum techniques in its design. Why not?
Spread spectrum is the technique of
transmitting messages by spreading the transmitted energy across a frequency
band. It was first used by the military
to defeat attempts by the enemy to jam our transmissions or intercept messages.
The enemy would try to jam a transmission by scanning a frequency band,
identifying a target transmitter, and then
transmitting at the same frequency to interfere with the receivers. By spreading
the energy, the transmitted signal was
difficult to detect. The wireless communications industry was interested
in finding other uses for this clever technique. Proponents of spread spectrum
reasoned that by using the technique, more users could be accommodated in
the
same frequency bandwidth. Although this was a controversial argument, it
nevertheless convinced some developers
to use spread spectrum in their equipment designs.
Would spread spectrum techniques improve the performance of wireless control
systems? Not for the type of
operations required by our customers. First, wireless control applications
do not have the operational uses that
would benefit from using spread spectrum techniques. There are not hundreds
of units in the same geographical
location competing for access. Second, spread spectrum does not improve
performance over current wireless
control systems. For controlling equipment at ranges less than 1,000 feet,
spread spectrum does not perform
better than normal packet communications at 900 MHz. That is because the
packet communications protocols
implemented by Patriot are effective in reliably delivering packets and
defeating interference in this frequency
band. This has been demonstrated repeatedly over years of experience in
real operational environments.
The one advantage spread spectrum does have turns into a disadvantage in
practical operation. The FCC permits
transmission at a higher power when in a spread spectrum mode. By taking
advantage of this FCC ruling, spread
spectrum systems can command equipment well beyond 1,000 feet. However,
this distance is also well beyond the
safe operational range for controlling equipment, and the capability to
operate at such a distance introduces an
additional safety hazard in operations. Patriot designed its wireless control
systems to meet the specific needs of
the industry and its customers with a special emphasis on safety.
Why not use spread spectrum for whatever additional value it may offer,
even if that value is marginal? With any
additional complexity, there are penalties. The use of spread spectrum increases
the power drain on batteries and
shortens the time between battery replacement or recharge. More complex
transmission algorithms also complicate
diagnostics. It is harder to determine the cause of problems with equipment
with spread spectrum algorithms. To
get the full benefit of frequency hopping spread spectrum technology, the
implementation must use a long sequence
of channels. The longer the sequence, the longer it takes for the receiver
to acquire or lock on to the transmitter
before it can transmit data. This not only delays operation when the units
are first turned on, but it also further
reduces the opportunity to decrease power consumption in the transmitters
by permitting frequent time-outs to
extend the operating life of the battery.
Our approach is to design for the intended use of the system, not for the
available technology.
Our equipment is fully capable of implementing spread spectrum algorithms
if and when our
customers need their unique benefits. |
|
Command
Pro Technical Note
Operating Reliability |
|
Some
equipment operators have experienced dropouts, or short periods
in which the transmitters dont work.
It is an annoying problem, but it also can be a dangerous one if you are
relying on the wireless control system to
keep equipment under control. Dropouts occur for a number of reasons. They
happen most often because the
operating frequency band chosen is noisy with interference, the communications
protocol was not designed to
handle unexpected interference from other sources of RF energy, or the physical
terrain causes a blockage.
The Patriot system was designed to minimize dropouts. We did that by selecting
the most appropriate frequency
band permitted by the FCC for license-free operation and then designing
a protocol and electronics that took full
advantage of the bandwidth to reliably deliver commands.
At 900 MHz, we operate well above the frequency of RF noise generated by
electrical equipment that is one
source of interference. But 900 MHz is still low enough to permit some bending
of our transmission around
physical obstructions. The following are key features of our design that
help further protect against dropouts:
Bandwidth Patriot Command Pro transmitters operate
in the 900 MHz band, where wide-band operation
is permitted. Many competitors operate in the 400 MHz band or at lower frequencies
where only narrow-band
transmissions using limited power are permitted. Bandwidth determines how
quickly data may be transmitted. The
narrower the bandwidth, the longer it takes to transmit the required data
to issue a command to the equipment. By
organizing the data into quick transmission bursts, we have decreased the
probability of disruption by interference
and increased the probability of successful reception. That is, we transmit
more redundant packets, which reduces
the probability of a noticeable dropout.
Power Our transmitters are designed for the
maximum power allowed by the FCC for use on the 900 MHz
band. The power authorized for fixed-spectrum transmissions is 1000 times
greater than the power level authorized
for other bands commonly used for license-free operation. The higher power
permitted by the FCC at 900 MHz
not only substantially increases the range of the transmitters, but also
overpowers interfering RF energy. A strong
signal at 900 MHz is like a strong FM station on your car radio. It will
be received loud and clear even if there are
weak signals present from any other source.
Decoding We have developed our own specialized
algorithms to decode commands from our transmitters.
These algorithms are designed to ignore interfering signals and to frequently
retransmit messages in order to increase
the probability of successfully communicating. Our special coding and signal
processing is specifically designed for
control of apparatus over radio waves without noticeable dropouts.
Antenna Polarization For especially noisy RF
environments, we have developed a specialized antenna that
is designed to ignore common sources of interference. Most interference
is vertically polarized. Our transmissions
are horizontally polarized. By designing an antenna that is horizontally
polarized, the effectiveness of the power of
interfering RF energy is greatly diminished. |
|
Technical
Note
Controller Area Network (CAN) |
|
|
|
The
Controller Area Network (CAN) bus is designed for communication between
microcontrollers. In an auto-
motive environment, it is used to exchange information between onboard Electronic
Control Units (ECUs) such as
the Engine Management System, transmission, instrument packs, and body electronics.
The German company
Robert Bosch GmbH originally developed CAN for the automotive industry during
the late 1980s. Its motivation
for the development of CAN was to provide a solution to the problem of the
enormous and constantly growing
wiring harness required for inter-ECU communication in modern vehicles.
The companys solution was to design a
single network bus to which all the on-board peripherals could be attached.
In 1993, CAN became ISO 11898
(the standard for high-speed applications) and ISO 11519 (the standard for
lower-speed applications). It is a multi-
master serial communications bus whose basic design specification called
for high speed, high noiseimmunity, and
error-detection features. |
|
|
|
|
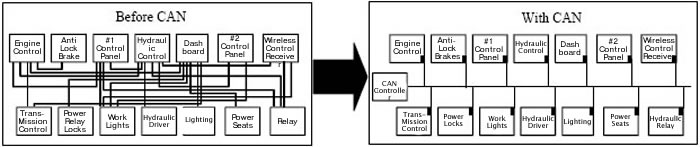 |
|
|
|
|
The CAN communications
protocol specifies the method by which data is passed between communicating
devices
on a CAN bus. It is the basic protocol (the first two layers of the sevenlayer
ISO Open System Interconnection
model) that permits the orderly transfer of messages in the data bus.
The transfer is managed by a CAN controller
that makes sure all network members have a chance to participate and resolves
any conflicts. To turn the messages
into useful information, a higher-order protocol (the seventh, or Applications,
layer) is also needed. The Application
layer protocols can be proprietary schemes developed by individual CAN
users or one of the emerging standards
used within particular industries. Common application layer standards
are DeviceNet, CANOpen, CAL, and SDS.
DeviceNet is especially suited to the networking of Programmable Logic
Controllers (PLCs) and intelligent sensors
and actuators. The application layer protocols also can provide centralized
diagnostics to permit quick isolation
of problems occurring in any node of the network. That is a major advantage
in the development
and maintenance of complex automotive systems.
The CAN Receiver (RCAN) supports the basic CAN protocol as well as some
of the application layer standard
protocols. Each manufacturer usually implements these protocols in a slightly
different manner in its equipment.
RCAN can be programmed to meet the specific requirements of each. By interfacing
through the CAN bus with
existing relays and drivers, the cost of duplicating these devices in
RCAN is avoided. This greatly reduces the
cost and complexity of adding wireless remote control to an automotive-type
system. |
|
|
|
Technical
Note
THEORY OF OPERATION |
|
The
Patriot Command Pro® equipment operates in the range from 902 to 928
Megahertz (MHz). A wavelength
at our frequency is 12.9 inches. The 400 MHz band used by most other manufacturers
has a wavelength of
29 inches. Like light, 900 MHz radio signals will pass through glass and
plastics, and will reflect off of walls,
buildings, and metal structures. Unlike light, 900 MHz radio signals will
penetrate all plastics, including those that
you cannot see through, thin-gauge steel, dry wood, dry concrete, plasterboard,
fog, and rain. Trees, earth, water,
people, aluminum, copper, and some window tints will not pass our signals.
Antennas convert radio signals into radio waves and convert radio waves
back into radio signals. They can send
and receive in all directions or in a single direction, depending on their
design. An omnidirectional antenna is like a
light bulb, and a directional antenna is like a flashlight. Metal objects
reflect radio waves, just as a mirror next to a
light bulb will reflect light. Metal objects near an antenna alter the intended
pattern of an antenna by either shading
or reflecting signals. Our standard antennas see equally well
in all directions. We have other antennas that will
see further in one direction for special applications. Our transmitters
and receivers are designed to have more than
a 2.5-mile operating range in free space (an unobstructed view).
Our systems are range-tested to 600 feet, and we
guarantee 300-foot performance. The extra signal strength provides a large
margin, which allows for reliable
operation in the presence of objects that can reflect or absorb radio signals.
The 902 to 928 MHz spectrum accommodates many license-free users and is
set aside by the FCC as an ISM Band
(Industrial, Scientific, and Medical). We have the ability to change frequencies
in this band and have 85 different
channels that we can assign to our transmitter and receiver. The actual
frequency is coded into the receiver and
transmitter at the factory but may be changed to one of the other 84 channels
in the field. Other devices in this
band include wireless phones, computer data links, and inventory equipment.
As a condition of using this band, we
must accept and handle interference from other users. The 900 MHz band has
worked well for most users, and not
being burdened with licensing regulations is always desirable. The FCC has
allowed 50,000 microvolts per meter
field strength on this band, which is 250 times higher than other unlicensed
frequencies below this band. This allows
our systems to operate very reliably in the presence of other signals.
We use Packet Mode Frequency Modulation to carry commands in a packet form
from our transmitter to our
receiver. To reduce battery drain, our transmitter transmits for a hundredth
of a second, which is long enough to
send one packet to our receiver at a repetition rate of 16 or 4 times a
second. The rate varies: 16 times a second
for three times when sending a command and four times a second when there
is no change in commands and the
transmitter is still on. Any time a lever or switch is activated, we send
all control settings three times at the
16-per-second rate and then return to the slower rate of 4 times per second.
Our receiver uses the slower rate for
maintaining transmitter timing and provides for a maintained link where
one is used. The only exception to this is the
STOP switch, which transmits at 16 times per second as long
as it is depressed. In addition to lever and switch
positions, each packet contains a unique address and CRC check sum (described
in the next paragraph). Safety
and preventing loss of control are very important issues at Patriot. We
use a unique identification code for each
user.
There are provisions in our system for 65,535 individual codes. Each transmission
includes a CRC check sum,
which is a polynomial created by factoring all of the previous bits transmitted.
Once our receiver receives a valid start
command from our transmitter, our receiver tracks the time of the transmitter
and ignores all other transmissions that
do not fall within the expected time frame of our transmitter. Maintained
link systems must receive at least one valid
transmission each second in order to allow the remote controlled equipment
to function. Our receiver provides a
loss-of-signal control output that safely shuts down the equipment if a
loss of signal occurs. Our receiver will not
allow restart of equipment under its control after a loss of signal until
a valid system start command is received from
our transmitter. This prevents an untended start-up from occurring if the
transmitter returns within range of our
receiver and is still operating. Our transmitters also check the position
of all controls upon start-up. Our transmitter
will not issue a start command if any of the controls are pressed at the
time the start command is invoked.
Exceptions for lights, horn, bell, or other user functions that do not place
machinery in motion can be mapped into
our control logic upon request.
The 900 MHz band has other users, but because we are only expecting a 300-foot
range, we have experienced very
little interference from other users. Spread-Spectrum and frequency-hopping
devices are used in this band. They are
allowed ten times the field strength that our transmitters are allowed.
Spread spectrum transmitters are required to
spread their power out over a large bandwidth (Spreading Code) and the maximum
power they can radiate in our
bandwidth is only a few percent of our allowed transmitter power. It would
take several of these devices close to
our receiving antenna to cause our equipment to go to the fail-safe mode.
Frequency-hopping devices are required
to use 50 or more channels, recognize other transmitters on frequency, and
hop over them. A frequency-hopper may
cause us to lose one command sequence from our transmitter, but because
each command sequence is sent three
times, our receiver will still receive each command sent. Radio waves diminish
as the square of the distance, so a
transmitter with ten times the power will be the same signal strength at
3.16 times the distance of our transmitter from
our receiver. FM systems also have a capture effect, where the strongest
signal will capture the receiver, which rejects
the weaker signal. The operator is seldom more than 300 feet from the equipment
he is operating. His transmitter is
the strongest signal present unless other equipment on this band is allowed
to operate within 1000 feet of the location
of the receiver.
In summary,we have developed a very robust proprietary digital communication
protocol that will survive the
harshest RF environment, including other signals present on the 900 MHz
band. |
|
Overhead Bridge Crane Remote
Control Systems, Remote Crane Control, Patriot Brand, 120 VAC Receivers,
Transmitter, Receiver, Two-Motion/Two-Speed Monorails, Three-Motion/Two-Speed
Cranes, and 4 or 5
Motion/Two Speed Cranes from your source for material handling equipment. |
Back to Product Category
|